Meet the team working around the clock to keep St. Michael’s Hospital running
The Supply Chain and Support Services department plays a crucial role in patient care
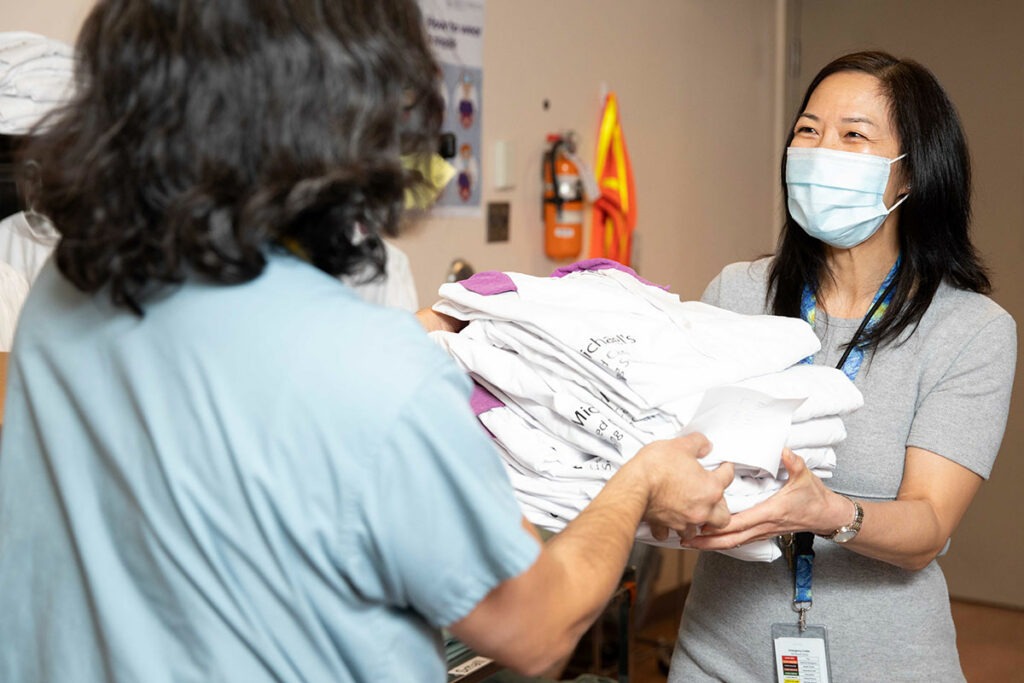
When you enter St. Michael’s for an appointment or surgery, you probably don’t realize that below your feet, in the basement of the Cardinal Carter Wing, is a mini army that maintains the day-to-day operations of the hospital. Evidence of their daily contributions are everywhere, from the scrubs worn by staff, to the posters on the walls, to the medications stocked on pharmacy shelves and carefully sterilized surgical tools.
The Supply Chain and Support Services team of 32 employees, two managers and three operations leaders provide a spectrum of services, including linen, shipping and receiving, stores, mailroom and the print shop. John Costa, Linen Operations Lead, has worked in materials management at St. Michael’s since the 70s. “We are an integral component of the whole machinery of running the hospital. I enjoy being involved in any aspect of the quality of patient care. The satisfaction I get from getting things done is what keeps me coming back every day.”
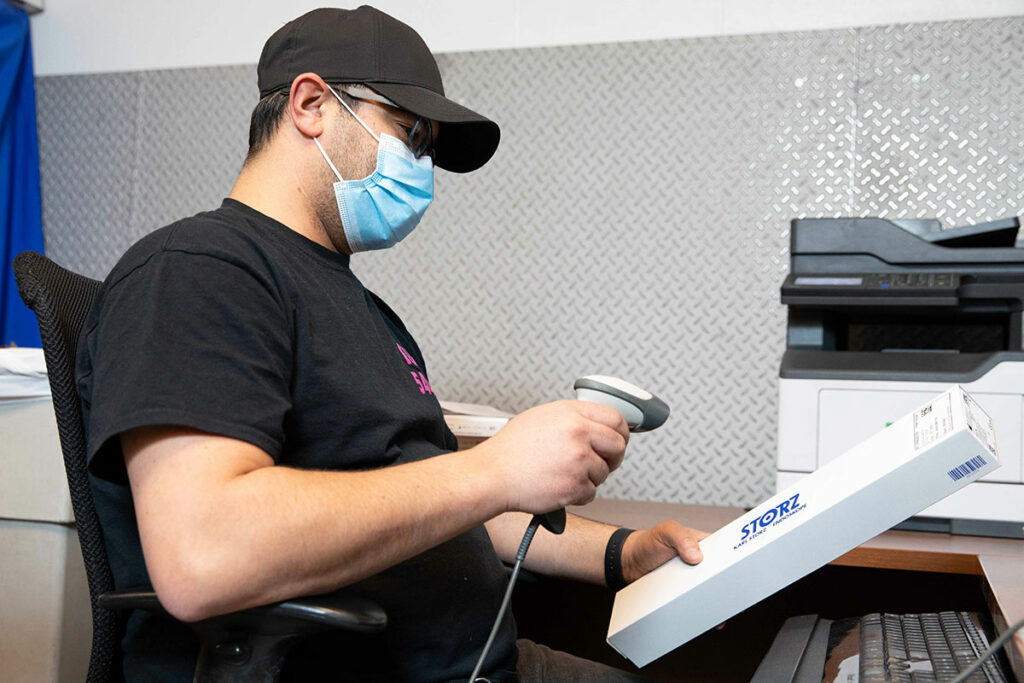
One the team’s major functions is receiving hundreds of daily shipments through the loading dock, where they are sorted and delivered – everything from fresh produce for the Marketeria, to medication for the pharmacy and medical supplies for patient units.
It’s a 6:30 a.m. start for Jason Amaral in the receiving office where he tracks all operating room materials. “We deal with a lot of tissue that needs to be refrigerated, surgical instruments, and items for elective surgery like ocular implants, knee and hip replacements,” he says. He scans everything that arrives into the system, makes sure enough supplies are on hand and works with the Medical Device Reprocessing Department (MDRD) to sterilize equipment and distribute them for surgeries.
“It’s paramount that we work together and avoid errors,” says Amaral, who supports around ten materials coordinators throughout the hospital including the Cardiac Catheterization Lab, Respiratory Therapy, and the Operating Room. “If we are missing something or our invoices are not properly reconciled, it directly affects patient care.” He has been on the receiving logistics team for eight years, which includes nine receivers, two dock personnel, a driver, and offsite receiving across the street at the Li Ka Shing Knowledge Institute.
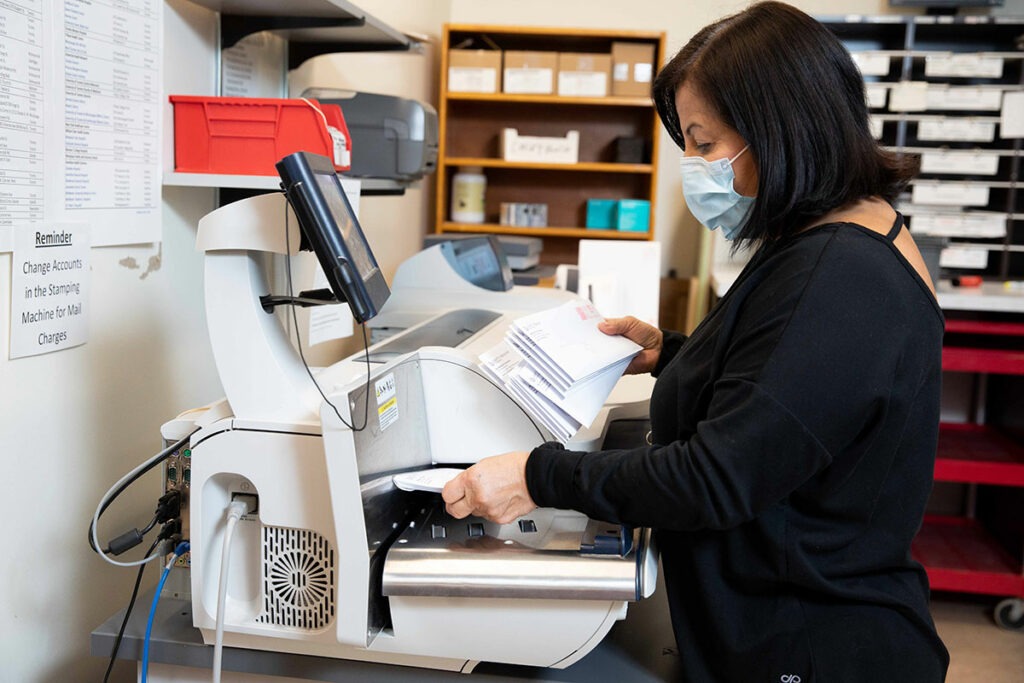
Carmenza Ospina, Logistics Assistant, is one of four staff in the mail room who handle all incoming and outgoing letters and parcels, including lab specimens. “Each morning we sort, stamp and deliver the mail that came in the previous afternoon. In the meantime, we do pickups across medical records, X-ray, lab work as well as offsite Doctors offices and community family health teams,” she says.
This team is responsible for distributing all communications between care teams and patients, from medical appointment reminders to lab reports. They process about 1,700 pieces of mail per day. “At the start of COVID there were many in-person appointments changed to virtual. Patients had to be informed so we were very busy mailing notifications on top of the emails that were sent. Our workload doubled.”
Ospina has been working at St. Michael’s for 22 years. “Our team gets along well and we help each other. I like to multi-task and that I am able to help everyone in the hospital in many different ways.”
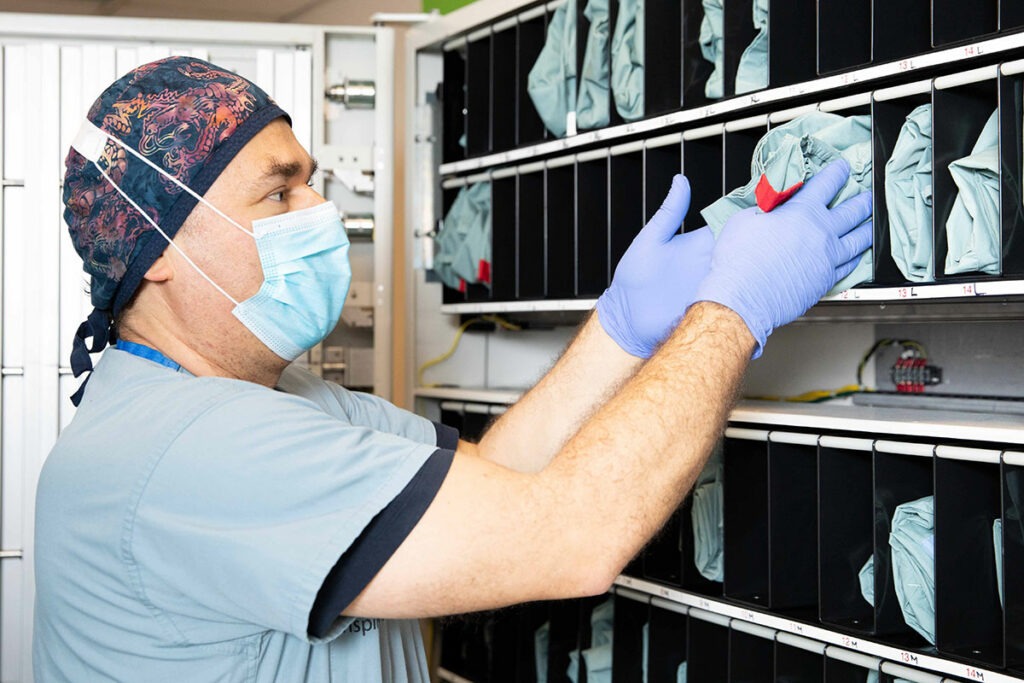
Theodoros “Ted” Coutoulas and the linen team ensure staff across the hospital have access to clean scrubs all hours of the day. “It’s collecting, washing, folding, loading. And it’s just go, go, go,” says Coutoulas, who has been on the team for ten years. In a 24-hour period, the linen team will typically launder 960 used scrubs. “I like that it’s a very physical job, the day goes by fast,” he says. During the pandemic, with the addition of screening and assessment centre staff, the number of people needing scrubs almost tripled to 4,741.
The team of 15 staff also launder lab coats, slings for patient lifting and patient mattress covers. Linens for patient beds are cleaned off-site and delivered overnight to each unit seven days a week.
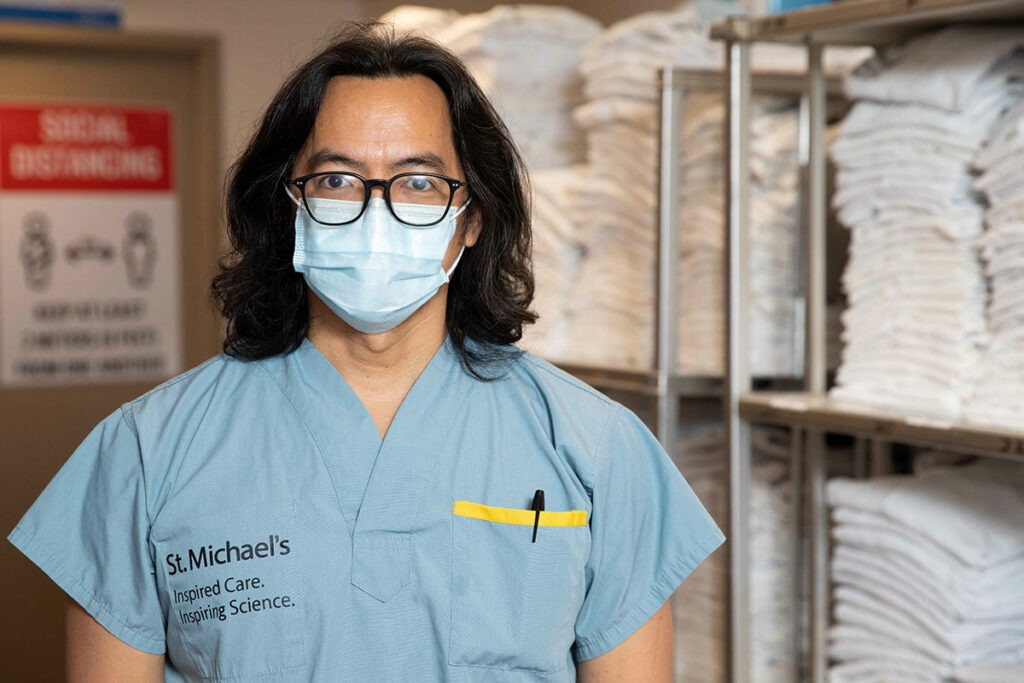
Marte Meneses, who has been at St. Michael’s for 30 years, works in central stores receiving. He signs up students, residents and new hires into the scrub system and supplies lab coats to doctors, nurses and researchers. “For me, St. Mike’s is home,” he says. “What I like about this job is the interaction I have with staff. It feels good to help them out.”
In the back of the department is a storage area where common items are available for all departments. “In Stores we carry everything from batteries, hand sanitizer, cleaning supplies, office supplies, to emergency power kits for staff,” says Meneses. On the patient care side they stock dressings for wound care, tracheal tubes, identification wristbands and medical forms such as blood lab requisitions. These supplies are regularly used throughout the hospital including Intensive Care Units, Operating Rooms and the Cardiac Catheterization Lab. “At the end of the day the most important part is the end of the line, which is the patient care,” says Meneses.
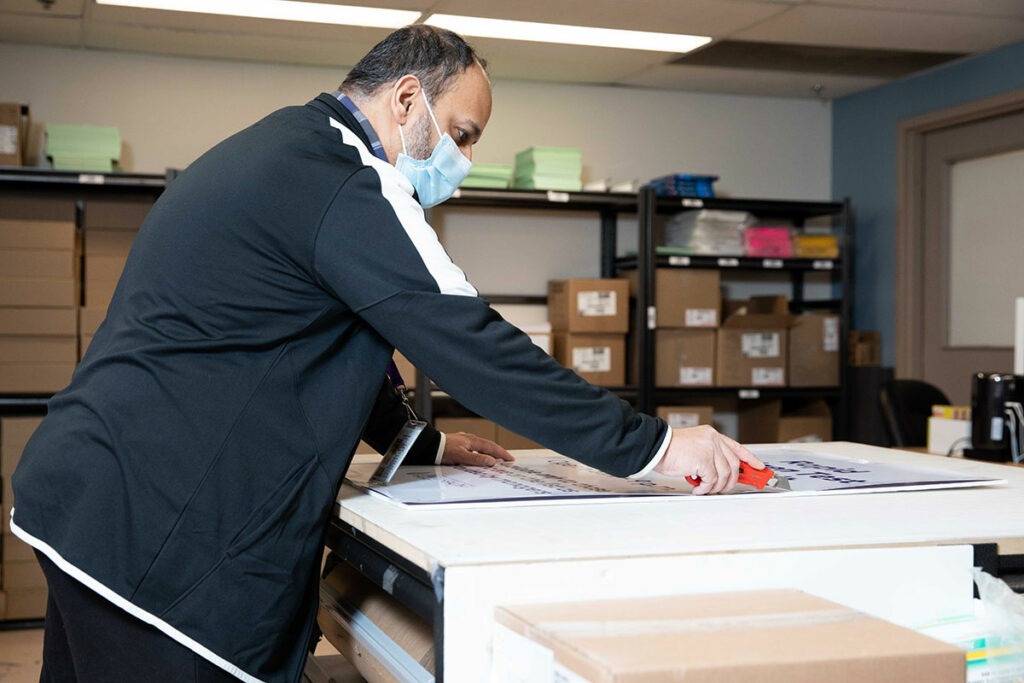
A unique aspect of support services is one of the last standing in-house hospital print shops in the Greater Toronto Area. “We make posters, forms, flyers, brochures, business cards, vouchers, labels; you name it, we’ve got everything here. We are a full-fledged print shop,” says Anwar Mohiuddin, who along with his colleagues Steve Edwards and Steve Abello, process around 19 requests per day. During COVID their workload doubled with an influx of directional and informational signage, visitor sticker labels for entrance screening, and signage for assessment centres and vaccine clinics across the three sites at Unity Health.
“We belong to and care for this organization and can pivot and prioritize requests as needed,” says Ed Robello, Operations Leader of Mailroom, Print Shop and PPE Supplies. “We take pride in the fact that an end user can come down the elevator within five minutes of placing a phone call and know their request has been received by a live person. And at a third of what it would cost from an outside vendor.”
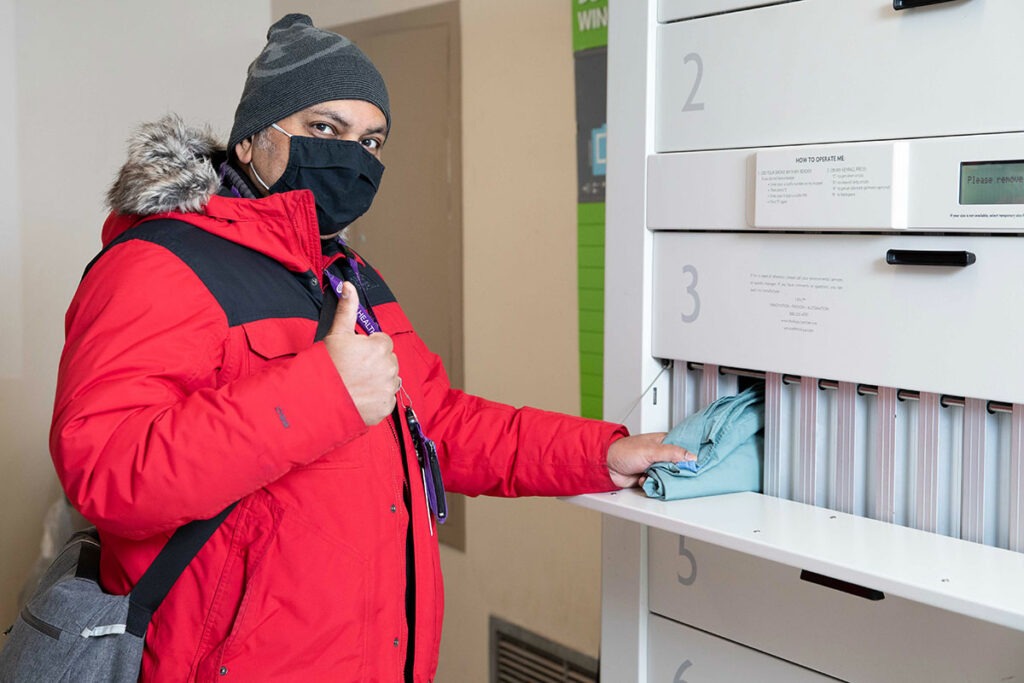
Sreenath “Nat” Rave, a Chiropodist in the Wound Care program, picks up his scrubs at the start of his shift. “I appreciate Ted and the team for keeping me clean and clothed,” he says.
Michelle Macdonald, Operations Lead of Materials Management, says the team takes pride in what they do.
“Just like at Disneyland, you never see them cleaning but it’s beautiful, right? Because they do it all behind the scenes. We’re kind of like that … everybody is conscientious and they understand that our work affects the outcome of a patients’ experience.”
Story and photos by Katie Cooper